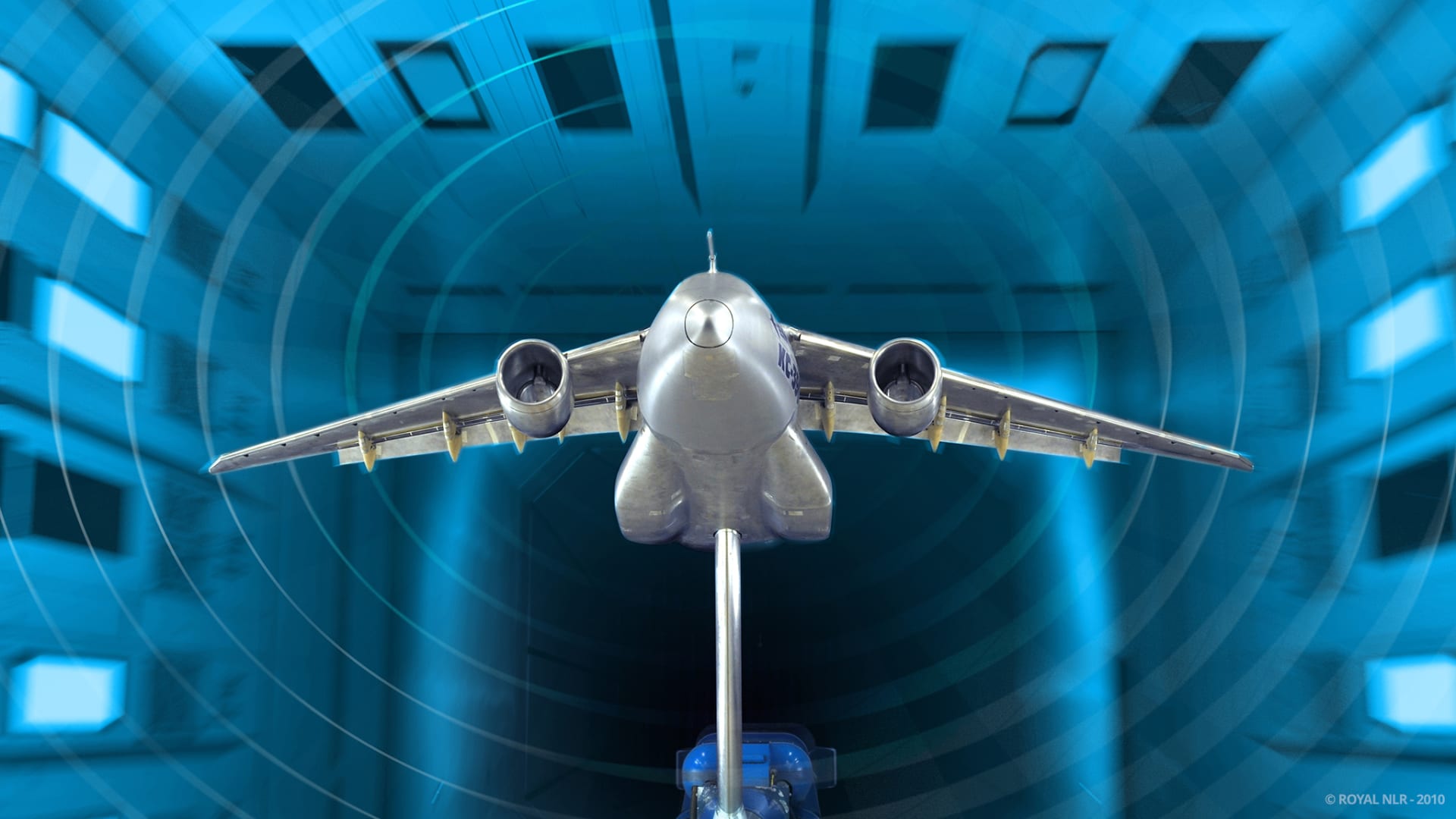
Induction Welding of Thermoplastic Composites: Numerical Prediction of Heating Patterns in Uni-Directional CFRP
- Hybrid
- Marknesse, Flevoland, Netherlands
- Aerospace Vehicles
Job description
Background of project?
Traditional joining methods of composite materials have several disadvantages. For instance, mechanical fasteners can locally damage the composite material and induce stress concentrations, while adhesive bonds require extensive surface preparations and the bond quality is difficult to control. Induction welding of thermoplastic materials enables a new joining method for composite materials. With induction welding these disadvantages are alleviated by re-melting the thermoplastic resin that after cooling down creates a perfect bond between two components. With a coil a strong alternating electromagnetic field is generated and because carbon fibres are conductors Eddy Currents occur in the laminate that result in heating. Induction welding of woven fabric composites is already well understood and applied in flying aerospace components. However, welding of Uni-Directional (UD) composites is more difficult to heat due to the architecture of the carbon fibres. Royal NLR is actively working on this topic to make induction welding of UD components possible. Numerical simulation of this process is used to increase our understanding of the process and assist the certification process.
Description of project
The goal of this project is to further develop our existing modelling methodology and use readily available experimental data for model validation. The modelling method is based on the Finite Element Method (FEM) and the commercial software package SIMULIA Abaqus is used. An electromagnetic model is used to predict the eddy currents and resulting Joule heating, which is coupled to a thermal model to determine the temperature evolution. First, the current modelling method will be evaluated based on experimental results. The second step will be to investigate possible improvements to better match the experiments.
Duration
This fulltime (graduate) internship starts preferably as soon as possible and will have a duration of 6-9 months.
Requirements
- A motivated student with a WO background in, for instance, aerospace engineering, mechanical engineering, or physics.
- Experience with FEM software such as Abaqus
- Affinity with composite materials
- Experience with Python is a plus
About NLR?
Royal NLR has been the ambitious research organisation with the will to keep innovating for over 100 years. With that drive, we make the world of transportation safer, more sustainable, more efficient and more effective. We are on the threshold of breakthrough innovations. Plans and ideas start to move when these are fed with the right energy. Over 650 driven professionals work on research and innovation. From aircraft engineers to psychologists and from mathematicians to application experts.
Our colleagues are happy to tell you what it’s like to work at NLR, make sure to watch this video!
This assignment will be performed within the Aerospace Vehicles Collaborative Engineering Systems department.
Want to know more or want to apply?
Contact Ir. Niels van Hoorn, R&D Engineer: niels.van.hoorn@nlr.nl; +31 88 511 46 93
or
All done!
Your application has been successfully submitted!